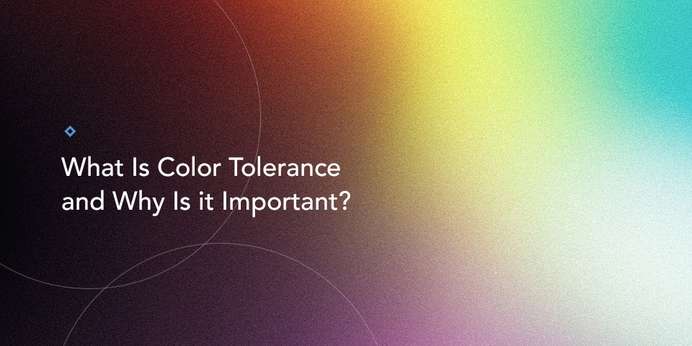
Color tolerances set acceptable limits for the appearance of a product and are an essential part of quality assurance and quality control processes for color. You can efficiently determine whether a product falls within the limits by establishing tolerances. If it does, the product passes. Failed goods fall outside the tolerances, meaning process adjustments may be necessary to create the desired appearance.
Many industries, such as food, plastics, and chemicals, rely on accurate appearance. Tolerances enable you to establish a standard and decide how much variation to allow, giving you consistent color outcomes.
What Is Color Tolerance?
Color tolerances are the parameters within which a product's color can vary yet remain acceptable. Typically, visual assessment is the initial step to define the acceptable color range. Spectrophotometry then objectively and scientifically quantifies and manages those tolerances.
Before establishing tolerance values, you must decide on the observer, choose a color scale, such as Hunter L,a,b, and then select illuminants for comparison, like D 65 and Illuminant A. Depending on what you're measuring, the scale you choose might come from the International Commission on Illumination (CIE), which sets global measurement standards, or from another entity.
Once you have a comparison standard, you can gather products and measure their color to determine acceptable variations called tolerance values.
In this process, you start by selecting a relevant standard for your product, then determine how much this standard can vary before it creates visible differences in appearance. This test helps you set boundaries for future production to objectively decide whether products fall close enough to the original standard to conform to quality expectations.
Detecting Color Differences
You can establish tolerances based on two levels of difference:
- Minimum perceptible difference: A visual comparison shows a just-noticeable difference between the standard and the sample.
- Maximum acceptable difference: The level represents the largest acceptable difference between a standard and a sample.
Focusing on the maximum acceptable difference means a broader range of acceptable values, while relying solely on minimum perceptible difference can lead to high rejection and material waste. As a result, choosing the right approach is typically industry-driven. For example, the food industry frequently uses the maximum acceptable difference, but pharmaceutical manufacturers usually opt for the minimum perceptible difference.
Range of Tolerance Definition
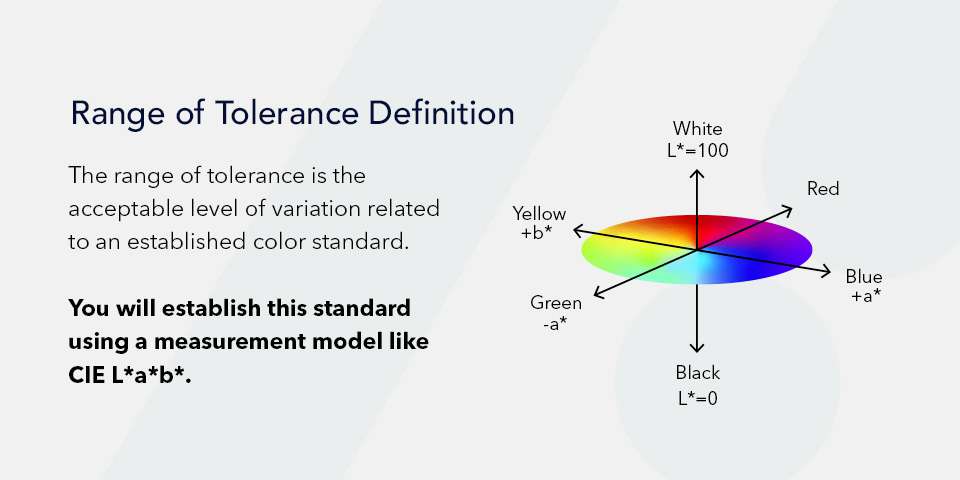
The range of tolerance is the acceptable level of variation related to an established color standard. You will establish this standard using a measurement model like CIE L*a*b*, which results in three values measuring:
- L*: Lightness, from dark at zero to light at 100.
- a*: Position on the red–green axis, with the positive number indicating red and the negative indicating green.
- b*: Position on the yellow–blue axis, with yellow represented as the positive and blue as the negative.
Once you establish a standard, you can decide on each dimension's tolerance. Here are the formulas for determining the difference (∆) between a sample and a reference:
∆L* = L*sample - L*reference
∆a* = a*sample - a*reference
∆b* = b*sample - b*reference
You can also calculate the total color difference across the three values in a single formula, with the results represented by delta E* (∆E*). Here's the formula to determine ∆E*:
∆E* = √((∆L*)2+(∆a*)2+(∆b*)2)
While ∆E* values can be helpful, use this method carefully. When the difference is spread over three dimensions, you may get a value that looks acceptable but has significant variation in one measurement, such as red vs. green.
This variation will create a noticeable visual difference but may not impact the delta E* value if the other dimensions are close to the standard. If you calculate the difference values separately, you can more closely monitor each one to verify that none stray too far from the standard.