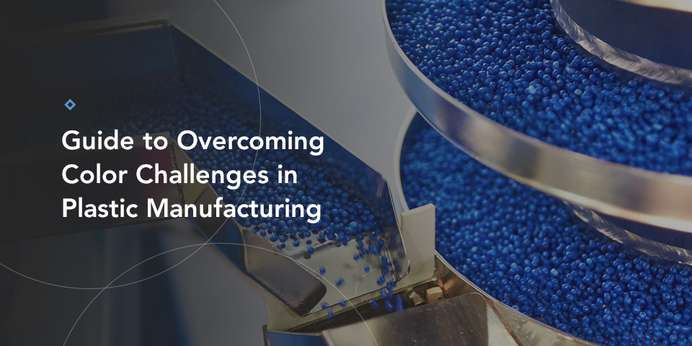
Plastic manufacturing has grown significantly since the 1950s, surpassing that of any other material. Today, plastics see use in markets ranging from automotive to goods packaging to food and beverage production. Plastic color is and will continue to be pivotal as the primary determinant by which consumers judge product quality and desirability, yet accurately quantifying it comes with unique challenges.
Common Challenges in Plastic Color Measurement
Typical plastic color measurement challenges include the following.
Natural Yellowing
Virgin plastic resins naturally yellow during processing as a result of oxidation. Additional yellowing can occur with age or exposure to ultraviolet rays. To achieve clear or almost clear end products, manufacturers must add optical brighteners that fluoresce on the blue side of the visible spectrum to negate the yellowness. That translates into almost all plastic goods containing at least some percentage of optical brighteners. As a result, these materials inherently fluoresce and introduce more complexity to achieving the desired clarity and visual chromatic qualities.
Regulatory Pressures
Government entities worldwide are passing ever-stricter regulations on the percentage of post-consumer recycled plastic that must be used in new plastic production to prioritize a more circular economy. An increase in the amount of recycled plastic used causes a corresponding rise in the amount of optical brighteners and other additives in feedstock that manufacturers must adjust for.
These challenges make accurate color measurements even more pivotal since one variation in the input can substantially impact the outcomes.
ESG Initiatives
In addition to governmental action, modern plastics manufacturers are feeling similar pressures from their stakeholders. Consumers, employees, and investors alike increasingly call for more sustainable practices and transparency in environmental impact.
To account for these pressures, many companies enact Environmental, Social, and Governance (ESG) initiatives that help achieve the six principles of a more circular economy. These pillars include minimizing waste, maximizing resources, saving energy, and reducing carbon footprint.
How to Resolve Color Measurement Challenges in Plastics
Fortunately, there are several steps you can take to resolve color measurement challenges with plastics production.